CleanSafe Services has been commissioned to clean production line extractor ducting in a food factory that makes Asian snacks.
The national food manufacturer called in a team of operatives based at CleanSafe Services’ Manchester depot to carry out the work as part of its regular clean down and maintenance programme.
The extraction system serves a deep fat fryer on a production line that runs 24 hours a day making spicy Indian snacks – so it has to undergo regular deep cleaning.
Ten skilled extreme cleaning operatives were deployed by CleanSafe Services to carry out the work during a planned 12 hour production shutdown.
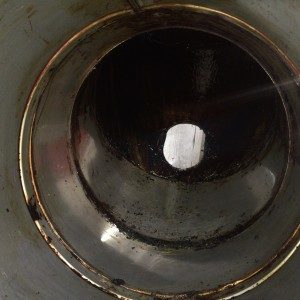
CleanSafe Services Business Development Manager Elaine Curran said: “The ducting was 50 metres long with a 40 metre horizontal section and two 5 metre risers.
“Cleaning such ducted extraction systems is essential, as a key element of fire prevention, hygiene control, and odour minimisation measures in food factories like this.
“It was critical that we completed the work during the 12 hour maintenance shift, so production was not disrupted. Given our experience, and capacity, as the UK’s leading extreme cleaning specialist, we could guarantee this would be done.”
The main task for the operatives was to remove oil and grease residue from the inside of the 500mm diameter circular extraction ducting using specialist scrapers.
The waste material was bagged up ready to be disposed of by the client.
Elaine Curran said: “CleanSafe Services was invited to tender for the work by the company, as it was aware of our expertise and experience in cleaning food production ducting systems to the highest quality standard.
“Like all responsible food manufacturers, our client sets extremely high hygiene and health and safety standards, which we could demonstrate with confidence that we would comply with.”